Ряд предпринимателей предпочитают сэкономить на производственном исполнении пульта управления гранулятором, смонтировав его собственными силами. Ну что же, таковое вполне возможно, имея чёткое представление о принципе работы гранулятора: запуск, вывод на режим, работа и останов.
Основная задача пульта — оперативное ручное или автоматическое управление параметрами оборудование на основании информации с контрольных точек, а также ввод уставок на основные узлы.
Решая этот спектр вопросов нам понадобиться подготовить внятное техническое задание на составление схемы пульта. Для этого начнём с описания самого принципа начала работы гранулятора:
- Проверить наличие подготовленного сырья в бункере-ворошителе участка гранулирования;
- Включение ворошителя бункера материала (не зависимо от гранулятора);
- Запуск системы смазки и контроля агрегата;
- Двигатель (двигатели) гранулятора. Выдержка по времени;
- Смеситель (кондиционер);
- Шнек-дозатор (дозатор сырья);
- Подача связующего (при наличии в технологии)
- Доувлажнение (пар, вода).
После запуска, при подаче сырья от 10 до 20% от номинала, настраиваем режим получения качественной гранули. Выводим агрегат на рабочее состояние, постепенно увеличивая подачу и контролируя параметры нагрузки, удерживаем качество получаемой продукции в заданных пределах.
Если параметры гранулирования резко отличаются от нормативных, а продукция выходит за рамки качества, то необходимо принять меры к их устранению: проверить параметры сухой массы, «запечатать» матрицу, проверить наличие и подачу влаги в смеситель, произвести регулировку вальцов.
Контролируемые параметры системы:
- Потребляемая мощность агрегата (нагрузка);
- Температура узла гранулирования;
- Качество гранул;
- Параметры смазки вальцов и подшипниковой части агрегата.
- Наличие/отсутствие металла на металлоуловителях (магнитах).
Останов процесса происходит в обратном порядке с выдержкой по времени для освобождения деталей узлов от массы:
- Равномерное уменьшение подачи сырья и доувлажнения до 10% от номинала;
- Отключение подачи связующего (при использовании);
- Останов подачи сырья шнеком-дозатором;
- Отключение подачи доувлажнения. Выдержка по времени;
- Останов смесителя. Выдержка по времени;
- Подача маслянистой смеси в рабочее окно прессующего узла. Выдержка по времени;
- Останов двигателей гранулятора;
- Отключение станции смазки (при наличии).
Открываем крышку узла гранулирования и очищаем рабочее пространство от избытков массы. Осматриваем все узлы агрегата.
Если отсутствует автоматическая, централизованная система управления всем процессом производства, то система управления комплекса должна комплектоваться распределённой системой управления: каждый функциональный участок линии управляется своим пультом управления, что делает процесс управления удобным, так как это позволяет операторам управлять производственным процессом в непосредственной близости от оборудования, а также, при наличии материала, работать каждым участком независимо друг от друга.
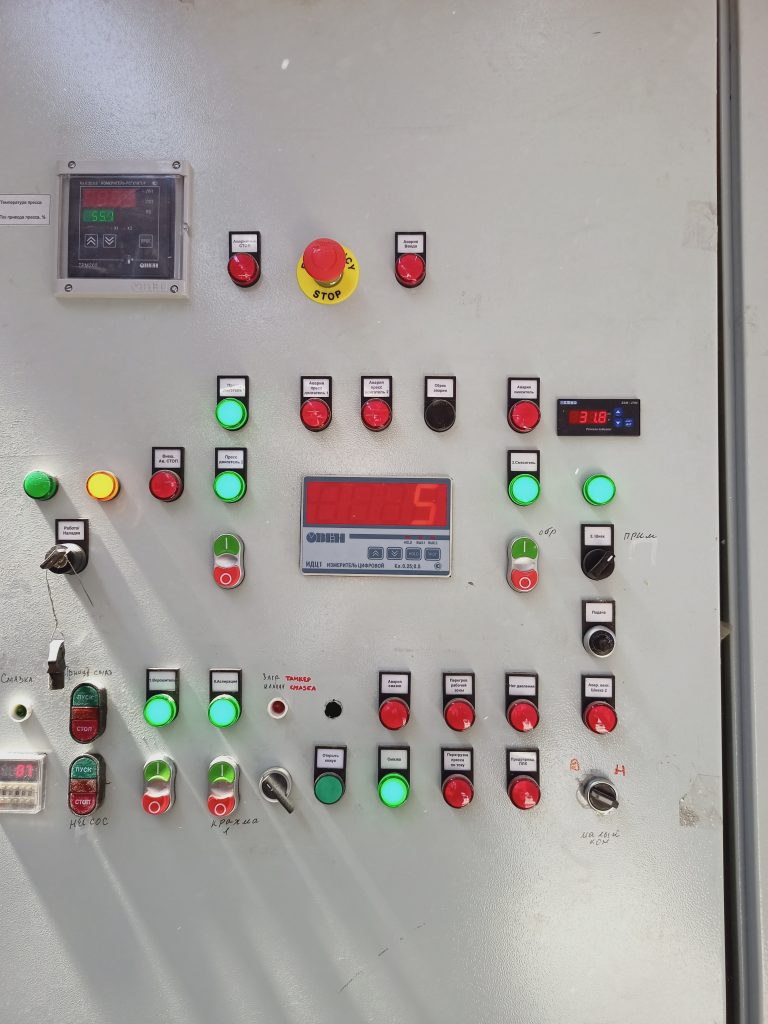
Пульт (ШУ) должен иметь несколько степеней защиты, предотвращающих возникновение аварийных ситуаций:
- Устройства тепловой защиты предотвращающие перегрев основных двигателей и перегрузку сети;
- Вводные автоматы по номиналу защищающие от коротких замыканий;
- На пульт управления выведены концевые выключатели от оборудования, прекращающие подачу электроэнергии в случае механических повреждений или несанкционированного доступа к работающему агрегату;
- Кнопка аварийного выключения позволяющая, в ручном режиме, выключить всё оборудование при необходимости;
- Блокировка пуска при нарушении последовательности запуска отдельных систем;
- Блокировка подачи доувлажнения (перекрытие клапана пара/воды) при остановке агрегата;
- Сигнализация замедления вращения вальцов.
Пульт управления (ШУ) гранулятором должен включать в себя следующие механизмы управления:
- Запуск/останов ворошителя приемного бункера-дозатора материала (не зависимый от системы управления гранулятором);
- Запуск/останов подачи связующего с частотным преобразователем (не зависимый от системы управления гранулятором);
- Управление двигателями, с контролем работы по амперажу или процентном отношении нагрузки (контроль перегрузки);
- Управление клапаном перегрузки (или шнеком подачи смеси по нагрузке);
- Управление скоростью смесителя (регулирование мощности);
- Регулирование нагрузки в зависимости от данных по току двигателей;
- Регулировка и управление дозированием;
- Ареометр подачи пара/воды (контроль подачи доувлажнения);
- Контроль вращения матрицы (с аварийным оповещением при замедлении);
- Контроль проворота вала при сломе предохранительных пальцев;
- Контроль температуры роликов (в случае если в грануляторе установлены датчики контроля температуры роликов);
- Запуск-останов станции смазки вальцов и подшипника с периодом подачи масла (управление смазкой);
- Контроль температуры рабочей зоны гранулирования;
- Запись и вывод сигнала тревоги.
И основное: комплексный пульт управления гранулятором, при производстве пеллет, должен быть удобен, достаточно информативен, надежен и прост в эксплуатации. Обеспечивать эффективную работу обслуживающего персонала, не требующего высокой квалификации.
Для большей наглядности, на дверцы пульта управления, если позволяет место, добавить наглядную схему процесса с индикацией рабочего состояния узлов. Если такового нет возможности воспроизвести, из-за ограниченного пространства, то, желательно, установить дополнительный щит в удобном месте контроля.
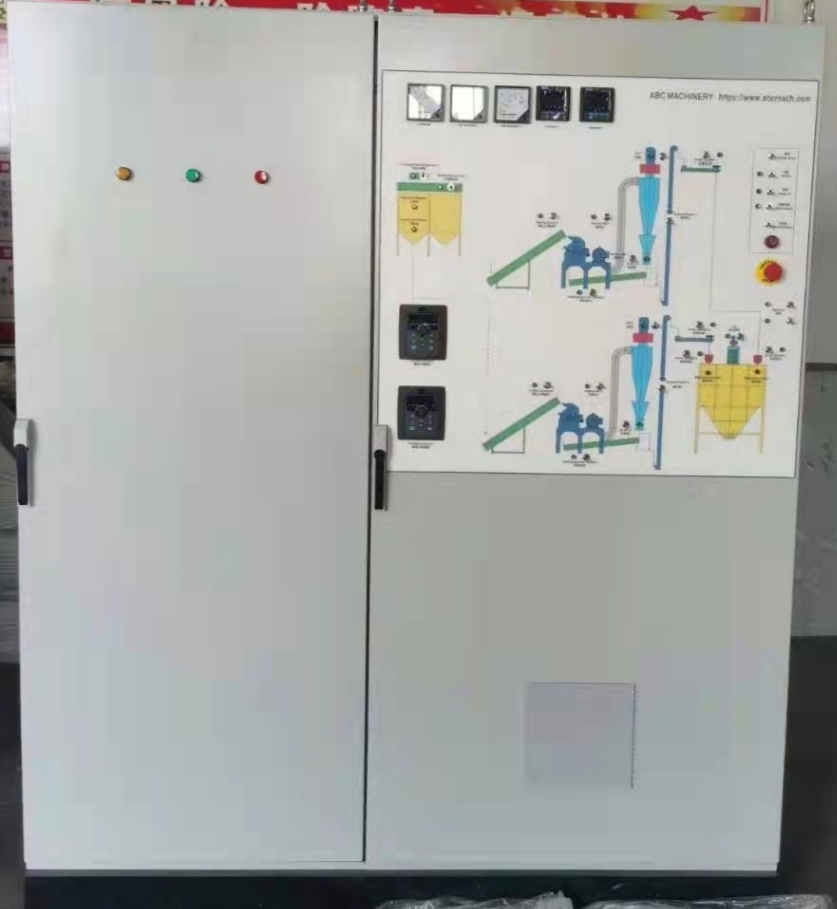
Если статья была интересной, прошу поставить оценку, оставить комментарии и поделиться ею в соцсетях, по значкам в нижней части статьи.
Свежие комментарии